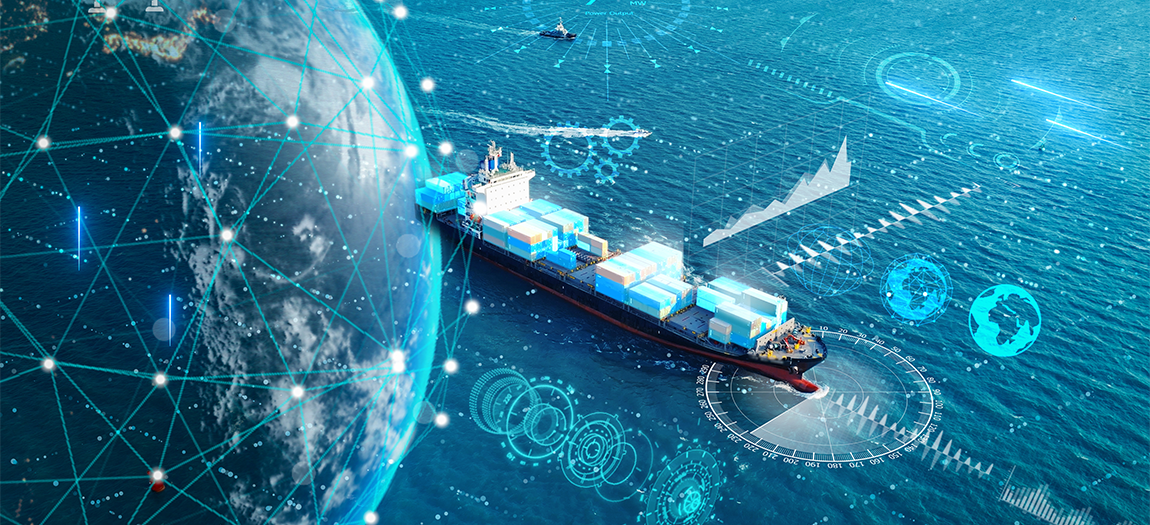
Geopolitical tensions, rising labor costs, trade barriers, intellectual property concerns, and the aftermath of the COVID-19 lockdowns are increasingly driving global companies to move at least some of their manufacturing operations out of China. According to a report by the Boston Consulting Group (BCG) released last year, it's a trend that will likely continue for the foreseeable future.
More than 90% of the North American manufacturers surveyed by BCG relocated some production from China in the past five years, and a similar percentage plans to make such moves in the next five years, with Mexico, Southeast Asia, India, Turkey, and Morocco the most likely targets. Investments in U.S. domestic manufacturing, spurred by the Inflation Reduction and CHIPS acts, are also fueling relocations.
While the primary driver of these shifts is cost savings, according to the report, companies are also looking to shorten lead times, operate in more stable business environments, and gain the flexibility to respond to disruption — even if that means a reduction in operating margin. The report does note, however, that only 55% of respondents say that their production moves have fully achieved their objectives — cost savings, better access to labor, or faster time to market — and that companies need to devise better comprehensive manufacturing and sourcing footprint strategies to realize those goals.
“Companies need to fundamentally rethink their manufacturing and distribution networks, build capabilities in new geographies, leverage government incentives, and establish new relationships across the supplier ecosystem to enhance their competitive advantage and protect their business,” wrote BCG’s Ravi Srivastava, coauthor of the report.
DIVERSIFICATION NOT DESERTION
Although companies are shifting a percentage of their manufacturing operations out of the People’s Republic, it is nowhere near a wholesale abandonment. In 2023, China still accounted for 31.6% of the total global manufacturing output — nearly double that of its nearest competitor (the U.S. with 15.9%), according to the World Bank. Instead, companies are employing a strategy known as “China Plus One,” which mitigates the risks of relying solely on China’s supply chain by diversifying manufacturing operations and expanding into other countries — while still maintaining a presence in China. The strategy gained traction about a decade ago due to rising labor costs in China and accelerated in 2018 due to the Trump administration tariffs (continued by the Biden administration, which later added tariffs on semiconductors and electric vehicles). Implementation of the strategy exploded when Beijing implemented its zero-COVID policy, wildly disrupting supply chains.
A significant number of global firms have relocated operations in recent years, with footwear companies Nike and Adidas steadily reducing their manufacturing presence in China and moving operations to Vietnam. Apple has been moving operations to India, as has Google, which plans to begin manufacturing Pixel smartphones to export them to the U.S. and Europe. Hugo Boss, which reached $4.6 billion USD in sales in 2023, is set to shift its production focus towards Europe and America to align its manufacturing operations more closely with its sales markets.
Companies need to fundamentally rethink their manufacturing and distribution networks, build capabilities in new geographies, leverage government incentives, and establish new relationships across the supplier ecosystem to enhance their competitive advantage and protect their business.
SUPPLY CHAIN DIVERSIFICATION CHALLENGES
Moving operations out of China offers many benefits, but the strategy is not without its challenges, cautions Tobias Schultheiß, SIOR, managing partner at German CRE firm Blackbird Real Estate GmbH. “In the short term, diversifying supply chains away from China will likely lead to increased costs for companies. The immediate logistical challenges of relocating manufacturing and sourcing parts from alternative suppliers can disrupt production schedules and increase expenses,” he notes. “For example, setting up new manufacturing facilities in countries like Vietnam, India, or Mexico involves significant initial investment and time, which could lead to temporary shortages of goods or delays in delivery.”
From a global perspective, the shift could lead to increased competition among emerging markets to attract foreign investment and manufacturing projects, and the push towards nearshoring could create new job opportunities and stimulate economic growth in regions that have seen industrial decline. “Countries like Vietnam, Thailand, Indonesia, and Mexico are poised to benefit as companies seek to diversify their supply bases. However, these countries may face challenges in scaling up their infrastructure quickly enough to meet the sudden increase in demand, which could lead to bottlenecks and capacity constraints in the short term,” he warns.
Schultheiß says that German companies are deeply integrated into global supply chains — particularly in the automotive and industrial sectors — but the recent geopolitical uncertainties and disruptions have many companies exploring options to reduce their reliance on Chinese suppliers. While the transition period could be challenging for German manufacturers, the long-term benefits will encourage companies to invest in advanced manufacturing technologies (such as automation and artificial intelligence) to maintain competitiveness and compensate for the higher labor costs.
ENERGY A FACTOR
One of the barriers to reshoring manufacturing operations to Europe is the energy shortage, as the invasion of Ukraine by Russia has significantly limited Europe’s access to Russian energy. “Energy costs have skyrocketed across Europe, which has made manufacturing more expensive and reduced profit margins…so some companies are moving production closer to their key markets to mitigate energy risks,” explains Schultheiß.
One of those markets is the U.S., where natural gas-producing submarkets are attracting manufacturers from Europe. Bryce Custer, SIOR, a broker/advisor with Canton, Ohio-based NAI Spring Commercial, says he is seeing more companies from Romania and Turkey and, more recently, from Italy and Spain in search of U.S. manufacturing locations. Custer spoke with several European companies at the 2024 SelectUSA Investment Summit (the U.S. government program focused on facilitating job-creating business investment in the U.S.) held this past June. Custer says that one of the primary reasons they were interested in relocating manufacturing to the U.S. was that the transition to renewable energy in the European Union (EU) is creating a scarcity of natural gas. Last year saw an unprecedented fall in fossil fuel use in the EU, with gas power falling by 19% and wind power generation (18%) overtaking gas (17%) for the first time, according to a report by independent energy think tank Ember.
“As we were talking to companies, they found that the Ohio/West Virginia/ Pennsylvania Appalachian area has an abundance of natural gas drilling and that they can locate their facilities right on top of the feedstock,” notes Custer. “We’re seeing quite a few of these European countries zeroing in on our area because their energy costs would be much less due to the lower cost of electricity.”
He also believes that energy savings, not labor costs, attract companies to the U.S. from China. “I may be stepping out on a limb here, but what I’m observing is that between the United States and China, the labor has become more of a level playing field,” says Custer. “I'm seeing more people wanting to come to the United States because of the natural gas and the natural resources because it's so much cheaper than it is in China.” (U.S. natural gas production reached record highs in 2024, while China is a significant importer of natural gas and LNG, resulting in higher prices).
Custer adds that companies that prioritize sustainability measures in their manufacturing processes are also looking to relocate to the U.S. In 2023, China accounted for 95% of the world’s new coal power construction activity, according to the latest annual report from Global Energy Monitor (GEM), and coal-powered electrical generation facilities account for more than half of the country's electricity — which is not consistent with the goals of companies implementing ESG strategies.
Manufacturers can significantly reduce costs, improve resilience, and enhance sustainability by strategically transforming their global manufacturing and sourcing footprints.
MEXICO BECOMES THE NEW CHINA
One country that has significantly benefitted from global firms' diversification strategy is Mexico, which is being dubbed “the New China.” Mexico and the United States share a land border, and Mexico benefits from the tariff exemptions granted by the United States-Mexico-Canada Agreement (USMCA). According to a report by BBVA Research and the Mexican Association of Private Industrial Parks (AMPIP), 830 new foreign firms relocated to Mexico from the beginning of the China-US trade war in 2018 to the close of 2022, and an additional 450 more are expected to set up shop by 2025. Tesla, Dell, and Unilever announced plans to open manufacturing facilities in Mexico in 2024, and Volvo announced last spring that it will build a new $7 billion heavy-duty truck manufacturing plant in Monterrey, Mexico.
“We have seen a lot of activity in our markets. A lot of companies that have a presence in Asia are relocating some of their production to Mexico to provide for the U.S. market. A lot of Asian companies, mainly Chinese, are looking to be closer to the U.S.,” says Baltazar Cantu, SIOR, an industrial director in the Monterrey office of Colliers International.
The auto industry is one of the primary industries relocating operations to Mexico — including, ironically, Chinese manufacturers. Since June 2022, 29 Chinese auto parts manufacturers and car makers have announced a combined $7 billion investment in Mexico. While the proximity to U.S. markets is a factor, Cantu says that many companies have barriers to entering the U.S. markets, “so they're focusing more on growing southward. They want to penetrate the Mexican market as well as the Central and South American markets.”
LOOKING AHEAD
According to the BCG report, manufacturers can significantly reduce costs, improve resilience, and enhance sustainability by strategically transforming their global manufacturing and sourcing footprints. However, this requires a comprehensive approach that includes regionalization, strategic partnerships, and leveraging government incentives. Companies can gain a competitive edge in the increasingly volatile global business landscape by proactively adapting to changing conditions and seizing on opportunities.

This article was sponsored by the SIOR Foundation - Promoting and sponsoring initiatives that educate, enhance, and expand the commercial real estate community. The SIOR Foundation is a 501(c)(3) not-forprofit organization. All contributions are tax deductible to the extent of the law.
CONTRIBUTING MEMBERS